Benefits of Modern Network Management for Gas
By Kevin Ruggiero & Tom DeWitte
PHMSA requires all gas and hazardous liquid system operators to maintain accurate and up-to-date records and/or maps of their pipe system. Records must include tests, inspections, and attributes required by the manufacturing specifications applicable at the time the pipe was manufactured or installed. Managing this information is foundational to pipe organization’s “knowing their systems”.
To truly “know your system” is more than simply managing information about pipes on a map or within a database. The organization needs to understand how the gas or hazardous liquid pipe system is connected and how the commodity flows through the connected pipe components. Every department within the organization is making decisions that require this knowledge. Even departments such as finance and legal, make decisions based on where the pipe is located and how the commodity flows thru it. Finance determines how much and who they owe taxes too based on where those pipe assets are located. Legal needs to understand who is downstream from a specific location to validate that service level agreements are being met.
Historically this information has been segmented and siloed, making it difficult for an organization’s departments and staff to easily access this information. These silos are often given names like distribution, transmission, storage, and gathering. Each represents a subsystem within the connected pipe network. This unnatural segmentation does not accurately represent the real-world pipe systems they are attempting to represent. Real-world pipe systems are fully interconnected. If these subsystems are owned by a single organization, we refer to that organization as being vertically integrated.
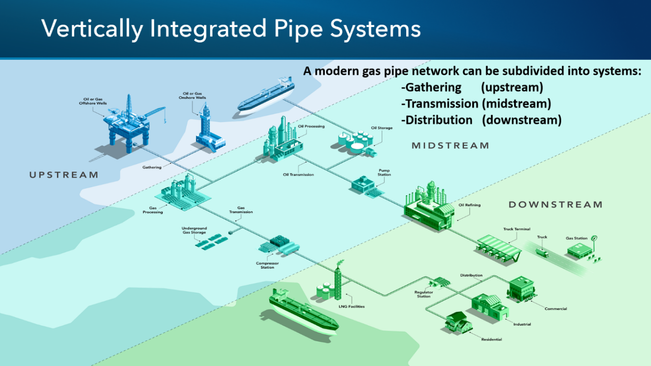
Managing digital information about these vertically integrated pipe organizations and how the gas or hazardous liquid commodity flows through them requires special capabilities. Special capabilities that enable an organization to model the entire pipe network from its extraction from a well to the final delivery of the product to the customer. Special capabilities to model this complex pipe network as ONE network. Special capabilities that are provided with ArcGIS.
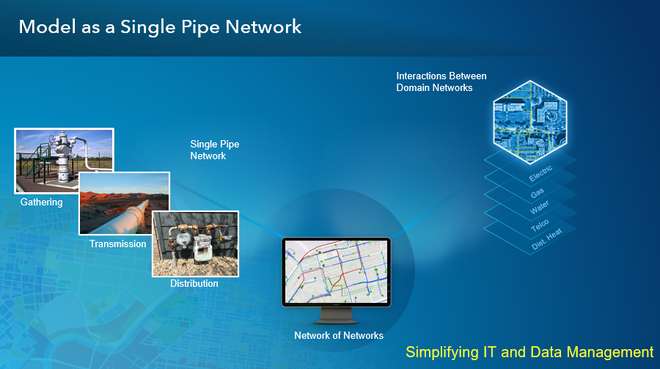
ArcGIS Modern Network Management
ArcGIS provides the many tools and capabilities required by those responsible for maintaining this information to build these digital representations of these pipe networks as a single Pipe Network.
For managing the connectivity of the assets across a single pipe network, ArcGIS provides a collection of tools and capabilities called Utility Network. Utility Network manages the connectivity between all assets.
When the transmission subsystem is a part of the single pipe network, additional tools, and capabilities to create and manage routes is required. This set of tools and capabilities is called ArcGIS Pipeline Referencing.
Organizing this information into one database where the assets can be modeled as a single pipe network with network connectivity, and linear referencing requires a well-organized data model. A data model that marries the Utility Network information model, with the ArcGIS Pipeline Referencing information model, and the asset information needed to correctly describe the pipe system’s components. This data model is called: Utility and Pipeline Data Model (UPDM).
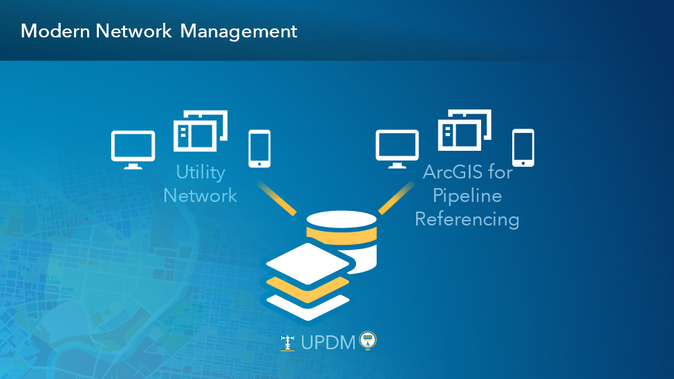
UPDM is the gas and hazardous liquid industry data model created, tested, and maintained by Esri.
Bringing together, Utility Network, ArcGIS Pipeline Referencing with UPDM provides a Modern Network Management system designed for today’s enterprise requirements.
Single Source of Truth
Leveraging services-based architecture, this modern network management system provides secure access to this data for the entire organization. A services-based architecture allows for a single point of access by applications and systems to this single pipe network. This eliminates duplication of data and the need for ETL’s (Extract, Transform, and Load). Now the entire organization can be confident that they are seeing the same information regardless of application or location. Everyone working off the same source data, whether you are in Engineering, Dispatch, Project Design, Planning, or operations. Everyone working off the same source of data, whether you are in the office or deployed to the field. Having the most accurate data available at all times, enables good business decisions and improved safety of your mobile workforce.
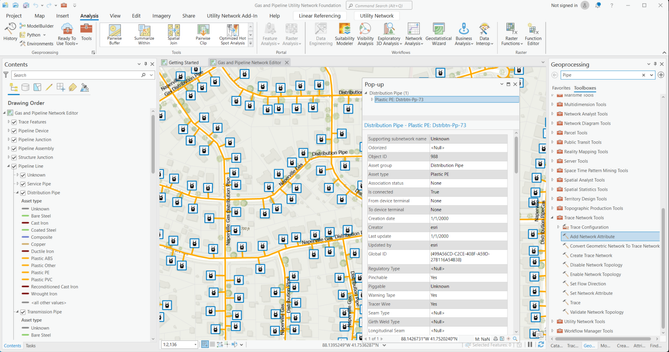
Accessing the same information across the organization
Managing Connectivity
Managing network connectivity is accomplished with the tools and capabilities of the Utility Network within ArcGIS. These tools allow natural gas and hazardous liquid organizations to not only connect their assets together, but to also accurately model the flow through those assets.
Utility Network tools enable designers and mappers to define, place, and connect all the assets of a pipe network. These connections can be based on spatial coincidence or a logical association. By creating logical associations, you can show how equipment is connected without having to spatially snap them together via spatial coincidence. Welded assets to be connected without drawing an artificial pipe segment between them. Anodes can be connected to pipes without having to draw the connecting wire.
Correctly assembling a network as complex as a natural gas or hazardous liquid pipe network, requires strong capabilities for ensuring data quality. ArcGIS provides the ability to define business rules is part of the toolset to help data creators to enter the information correctly the first time. Within ArcGIS we use terms like network rules, contingent values, coded value domains, and attribute rules to name the capabilities provided to implement business rules. UPDM provides configurations of these capabilities which are specifically configured for pipe networks.
The Utility Network tools include validation against the rule base. This ensures that editing is consistent within your organization. Validating your edits becomes part of your workflow. This ensures that the data being posted to your utility network has passed all the rules.
Attribute rules allow an almost endless ability to define custom rules for assets and structures within your network. These practices ensure that the data being entered into the utility network is accurate.
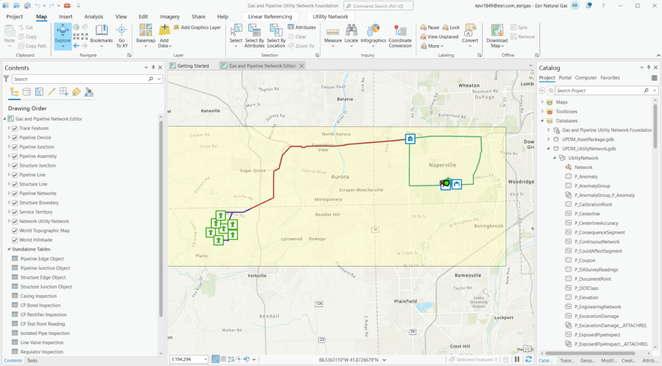
ArcGIS Utility Network is configurable for any utility, municipality, or organization with linear assets. Esri solutions explore the world of electric, gas, and water utilities, architecture, engineering, construction (AEC), and telecommunications.
Analytics
Pipe networks tend to be looped and interconnecting to improve reliability. Understanding how your commodity traverses your pipe network is challenging. ArcGIS provides tools called Trace tools, which leverage the connectivity to help organizations understand how your commodity traverses your pipe network. Trace tools provide the analytical capability to enable your organization to understand which customers are downstream of a location, where the gas or liquid originates from, and most importantly what valves to close to isolate a section of pipe. These trace tools are part of the geoprocessing framework within ArcGIS. This means the results of a trace can be incorporated into multi-step analytics within ModelBuilder or scripted within a python script. This opens new understandings for risk analysis and main replacement prioritization, such as tabulating for each pipe segment the number of critical facilities and the number of customers impacted by the failure of a pipe segment.
More on these capabilities can be found here: ArcGIS Utility Network | Spatial Information Management System for Utilities (esri.com)
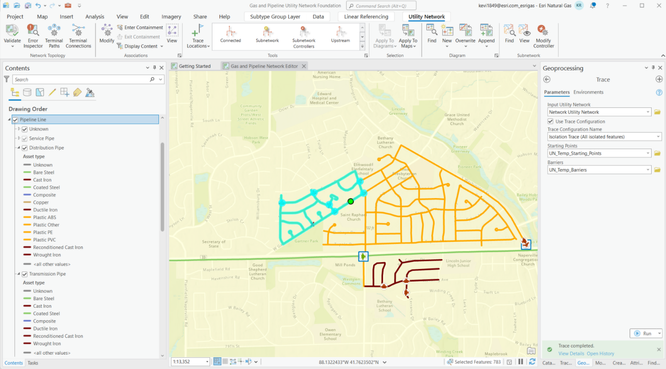
In this image is the result of a Distribution Gas Isolation trace.
Viewing Complex Facilities
When accurately modeling your pipe network, you will find portions of your service area where the map display can be crowded or cluttered. In these locations such as regulator stations, compressor stations, and even multi-meter buildings such as apartments, you need more intelligent feature display controls than most map viewing software can provide. For these feature-dense locations the ArcGIS Utility Network tools and capabilities, provide an additional feature display capability called Containers. Containers allow office and mobile users to initially see a simplified representation of the facility. For most data viewing activities simply knowing where the regulator station, compressor station, or wellhead is located is enough. But there will also be situations where the office or mobile user requires an understanding of the assets within the facility. Situations where the user needs to open the container to see the assets contained within the facility. Containers provides the feature display control capability to hide the assets within the gas or hazards liquid facility until the user decides they need to see what is within the facility.
Access from Anywhere!
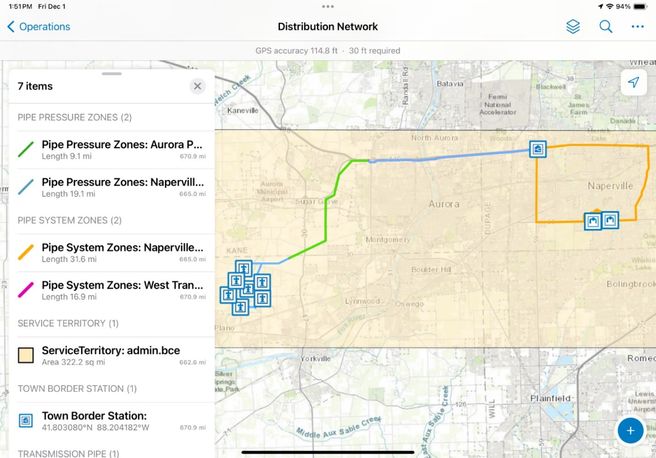
Accessing the same data accessed through ArcGIS Field Maps. Users in the field are looking at the same data as you are in the office, the same data, across the enterprise.
Pipe organizations require the ability to access their pipe network data from anywhere, anytime and on any device. The services-based architecture of the Utility Network provides the infrastructure to enable pipe organizations to meet this need. This single source of the truth allows office users of web applications to be able to answer their questions about the pipe network and how the commodity flows thru it. Using a web application, engineers planning maintenance which will require disruption of service can run traces to understand what valves to close and which customers are impacted. Mobile workers also have access to these same web services and capabilities on their mobile phones, tablets, and laptops. Using a mobile application such as FieldMaps an operations supervisor can run the same traces as the office staff to understand the impact and required response to a system outage.
Having access to the latest accurate data protects lives and safety for anyone who access or uses this data to perform their jobs. From the field to the office, everyone is using the single source of truth.
Integrated with Industry Solutions
Outage Management Systems (OMS), SCADA, CSS, Hydraulics, Pipe Calculators, Meter Reading, AMR, just to name a few, can be integrated into one system and accessible to those departments that need this information to perform their jobs. By integrating these systems together, agencies within your organization can be visualizing the data as it’s being collected and analyzed.

Provide integration of Industry specific applications. As shown in this image, Integration between ArcGIS Enterprise and Gas/Pipeline Industry Applications and made available to your organization.
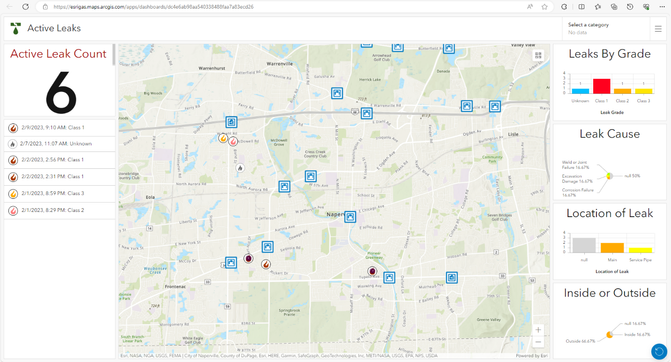
This is an image of an ArcGIS Dashboard configured to show Leak Information. Data is compiled together to show both Enterprise Utility Network data as well as Leak data being captured out in the field.
In Summary
Implementing an ArcGIS Utility Network for your organization provides your office and mobile workers with the ability to understand and explore the assets and connectivity within your pipe system. Utility network supports the utilities need to deliver their commodity safely and economically with efficient tools and rules that conform to the operations of your organization. Capturing the data accurately and having that data available to your organization provides the document of record for your organization or the single source of truth, everyone working off the same data. Working with a high-performing model that is scalable and enforces the integrity of your organization, allows for both small and large utilities to take advantage of the benefits of the utility network. For more information, please visit our GIS for Gas Utilities website: GIS for Gas Utilities | Natural Gas Distribution Mapping & Analysis (esri.com)